Best possible solder paste application
Description:
Best possible solder paste application. Photo taken with high magnification.
Causes/Remedy:
- -/-
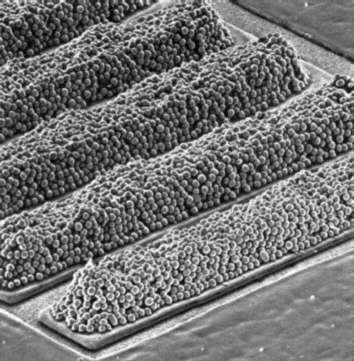
SEM
Bridge due to solder paste
Description:
Bridging between the solder paste depots. There is a high risk that bridges also form between the contacts during soldering. Rework necessary.
Causes/Remedy:
- unsuitable solder paste
- processing conditions ignored: temperature, best-before date exceeded
- poor printing process
- lifting-off stop takes solder paste with it
- contaminated stencil
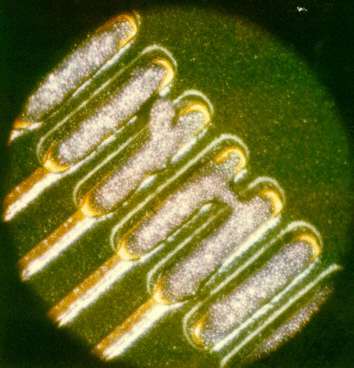
visual, optical inspection - general view
Uneven application of solder paste
Description:
Uneven application of solder paste. The amount of solder paste applied is clearly lower on the right side. This risks on non-soldering or insufficient solder. Rework necessary.
Causes/Remedy:
- unsuitable solder paste
- processing conditions ignored: temperature, best-before date exceeded
- poor printing process
- lifting-off stop takes solder paste with it
- contaminated stencil
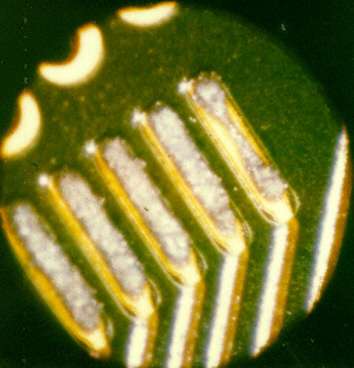
visual, optical inspection - general view
Uneven printing of solder paste
Description:
Again uneven printing of solder paste, but clearly less risky as far as insufficient solder or opens are concerned. Acceptable to a certain extent
Causes/Remedy:
- unsuitable solder paste
- processing conditions ignored: temperature, best-before date exceeded
- poor printing process
- lifting-off stop takes solder paste with it
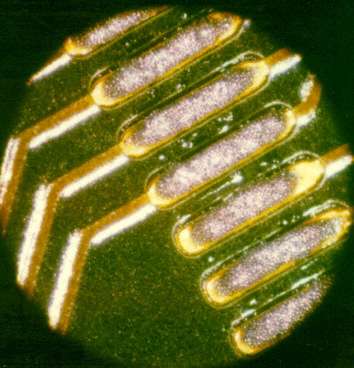
visual, optical inspection - general view
Description:
Uneven printing of solder paste. Spilling caused parts of the solder paste to reach onto the solder stop.There is the danger of bridges or microballs forming during the reflow process. Rework necessary.
Causes/Remedy:
- unsuitable solder paste
- processing conditions ignored: temperature, best-before date exceeded
- poor printing process
- lifting-off stop takes solder paste with it
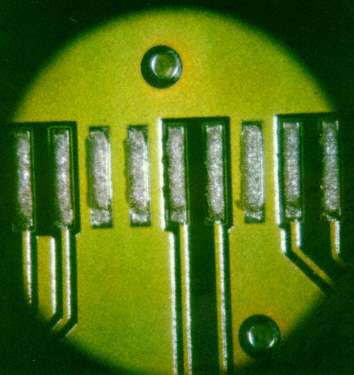
visual, optical inspection - general view
pulling up of solder paste
Description:
Pulling up of solder paste, forming of studs. Lifting-off the stencil takes solder paste with it. Es entstehen nach oben gezogene, spitze Zapfen. Acceptable to a certain extent, as long as no bridges generate or the amount of solder paste is drastically reduced.
Causes/Remedy:
- unsuitable solder paste
- processing conditions ignored: temperature, best-before date exceeded
- poor printing process
- lifting-off stop takes solder paste with it
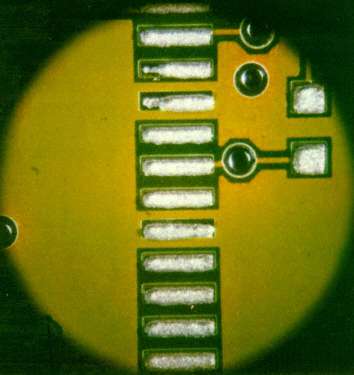
visual, optical inspection - general view
Smeared solder paste
Description:
Smeared solder paste. Solder paste is evident on the solder stop on the side of the printing area. Danger of microballs forming
Causes/Remedy:
- unsuitable solder paste
- processing conditions ignored: temperature, best-before date exceeded
- poor printing process
- lifting-off stop takes solder paste with it
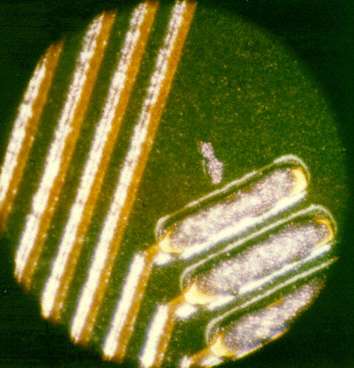
visual, optical inspection - general view
Contamination of the solder paste depot
Description:
Contamination of the printed solder paste depot. Textile fibres are lying on the solder paste. It could be proven that the fibres stem from textile material used to clean the stencil.
Causes/Remedy:
- unsuitable solder paste
- processing conditions ignored: temperature, best-before date exceeded
- poor printing process
- lifting-off stop takes solder paste with it
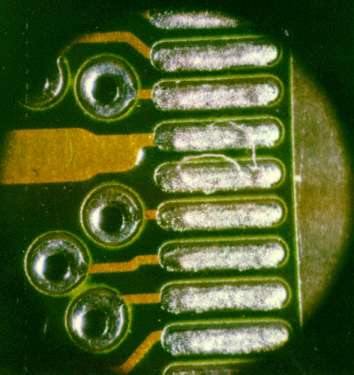
visual, optical inspection - general view
Description:
Contamination on the printed solder paste through flux residues (flitter). Moreover there is a slight (acceptable) printing misalignment of the solder paste.
Causes/Remedy:
- unsuitable solder paste
- processing conditions ignored: temperature, best-before date exceeded
- poor printing process
- lifting-off stop takes solder paste with it
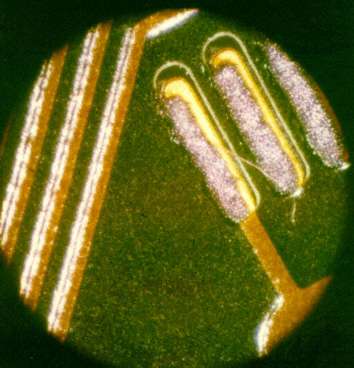
visual, optical inspection - general view
Excess solder paste
Description:
Excess solder paste on the pads (excess printing). The use of unsuitable printing stencils led to this excess printing. In some rare cases this is even intended for special types of components. For fine-pitch components there is the danger of solder bridges forming, however.
Causes/Remedy:
- unsuitable solder paste
- processing conditions ignored: temperature, best-before date exceeded
- poor printing process
- lifting-off stop takes solder paste with it
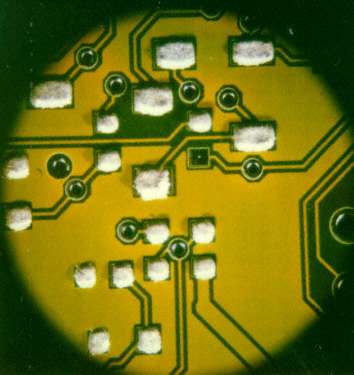
visual, optical inspection - general view
Our analytics team can help you find the cause.
go to failure analysis at TechnoLab