Lean solder fillet below specification limit.
Attention ! Always compare with current specifications and standards. They often differ from each other. Here DIN EN 61191, Part 1 - 4, and IEC 61191, Part 1 - 4 respectively are taken as reference basis. The assessment of all solder joints is based on the standards given above.
Insufficient solder at CMC
Description:
Reflow soldering of a 1812 CMC. In this case the layout caused a joint where the solder can be suspected to be insufficient. This soldering result is a borderline case according to IEC 61191 - 2 (Class A and B), however, and thus acceptable. Only for Class C is this solder joint insufficient and thus unacceptable. The fact that the solder joints do not cover the total width of the component suggest faults in dimensioning the pads.
Causes/Remedy:
- poor layout design
- use suitable components
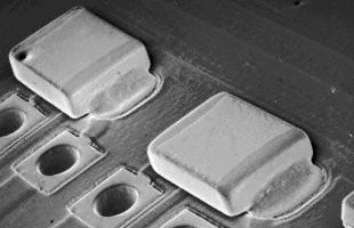
SEM
Description:
Insufficient solder in accordance with IEC 61191 - 2. The minimum height of the solder, i.e., one fourth of the component height, has not been reached. Moreover the wetting is incomplete over the totel width of the component. Rework is necessary. Observe soldering temperature (≤ 350 °C)
Causes/Remedy:
- wave soldering: bad wettability pad/component
- wave soldering: shadow effect/ layout design
- reflow soldering: poor solder paste application
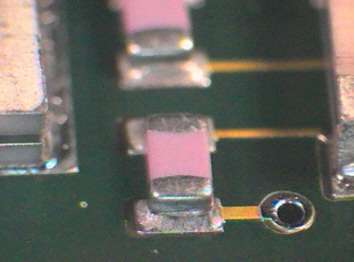
visual, optical inspection - general view
Description:
Borderline case of a reflow soldering joint at a CMC 1206. According to the standards wetting is okay and the requirement that the solder joint has to reach over at least one half of the component's width is fulfilled. Rework is not necessary. It should however be examined why such a shape could come about, whether this is a coincidental or systematic deviation.
Causes/Remedy:
- poor solder paste application
- wetting problems at the component
- process fault: tool life of solder paste exceeded
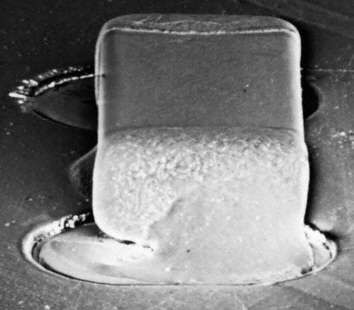
SEM
Insufficient solder at MiniMELF
Description:
Borderline case for insufficient solder in accordance with IEC 61197 - 2 (Class A and B). This solder joint can be accepted as a borderline case when compared with the other solder joints. It has to be checked, however, whether this is due to a systematic fault or incidental. A complete wetting of the component has to be discernible in principle. Therefore rework is not necessary.
Causes/Remedy:
- wave soldering: shadow effect, unfavourable position of component
- reflow soldering: poor solder paste application
- disturbed wetting at end of component
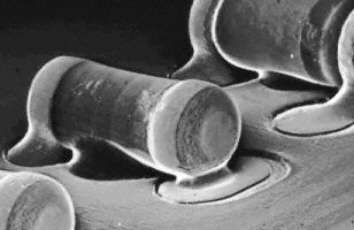
SEM
Description:
Borderline case of a reflow solder joint at a MiniMELF. This solder joint meets all minimum requirements of IEC 61191 - 2 in all classes (Class A-C). Wetting is irreproachable and the height of the solder fillet is 1/4 of the component diameter. No rework necessary.
Causes/Remedy:
- solder paste quantity relatively low
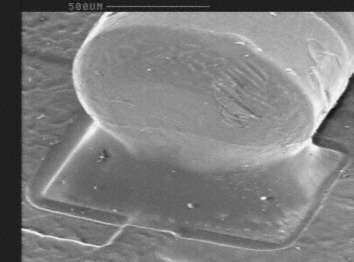
SEM
Description:
Same context as described above. Illustrated in colour for better understanding.
Causes/Remedy:
- solder paste quantity relatively low
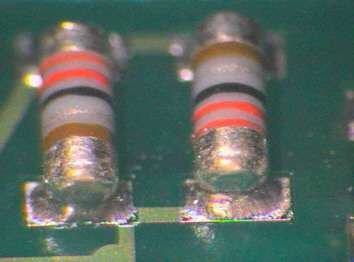
visual, optical inspection - general view
Description:
Same context as described above. Apart from that the photo shows a case of non-soldering (left) and a borderline case of insufficient solder. It can be seen how complex it is to analyse defects in the inspection of soldered assemblies.The difference between the two defects is difficult to define.
Causes/Remedy:
- wave soldering: shadow effect, unfavourable positioning of component
- reflow soldering: poor solder paste application
- wetting problems at component terminal end face
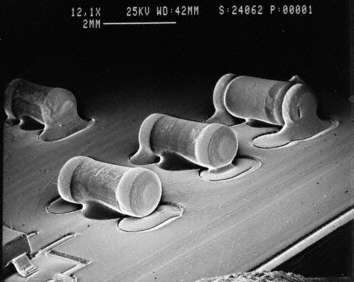
SEM
Description:
Borderline case of insufficient solder at a MiniMELF (center). The difference between the "normal" solder fillets (right) and the borderline case is clearly visible. In this case rework is not necessary. Indications concerning the quality and reliability of the solder joint cannot be deducted, however. But lean solder joints, in some cases even very lean solder joints have often proved to meet reliability requirements.
Causes/Remedy:
- reflow soldering: inhomogenous solder paste application
- wave soldering: wetting problems, shadow effect, flux problems
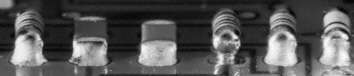
visual, optical inspection - general view
Insufficient solder at PLCC
Description:
For the minimum requirements of Class A this example can be regarded as a borderline case for insufficient solder. For the higher requirements of Class B and C the solder joints (middle, left) must be regarded as having insufficient solder and must therefore be reworked. The principle for J-leads is: The toe as well as the heel of the lead have to have solder fillets which show immaculate wetting.
Causes/Remedy:
- Reflow soldering: too few / poor solder paste applied
- Wave soldering: shadow effect
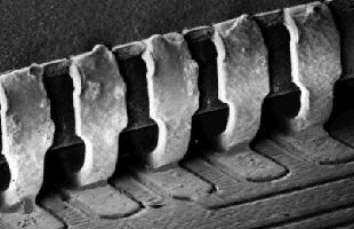
SEM
Description:
Same context as above. General view with improved lighting.
Causes/Remedy:
- reflow soldering: insufficient/poor solder paste applied
- wave soldering: shadow effect
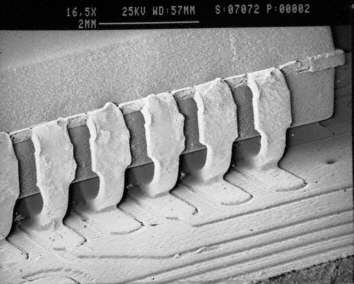
SEM
Description:
The above example from a different angle. The requirement concerning which a solder fillet has to show at the heel and at the toe, is fulfilled. Borderline case for insufficient solder (Class A) according to IEC 61191 - 2.
Causes/Remedy:
- reflow soldering: insufficient/poor solder paste applied
- wave soldering: shadow effect

SEM
Insufficient solder at SO
Description:
Reflow soldering of a SO with gullwing-leads. The photo shows very lean solder fillets which are a borderline case for insufficient solder. The properly wetted solder fillets are clearly visible. But the following principle also applies: There has to be a visible solder fillet at the heel of the lead. For leads of Alloy42 the higher-ranking acceptability class should always be taken as reference, since the joining partners normally have worse wettability properties than with other materials.
Causes/Remedy:
- Reflow soldering: too few / poor solder paste applied
- poor wetting properties
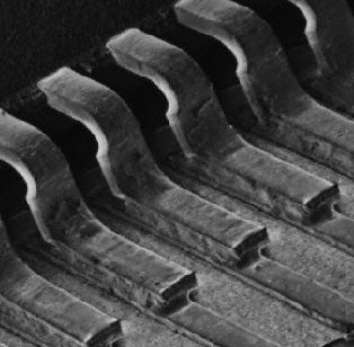
SEM
Unterbelotung bei SOT23
Description:
A processing fault before soldering (adhesive on the pad) caused a solder joint with insufficient solder. The solder joint has be to cleaned of the adhesive and properly reworked. It has to be made sure that there es a solder fillet at the heel of the lead.
Observe precautions for handling ESD!
Causes/Remedy:
- faulty solder joint due to adhesive on the pad
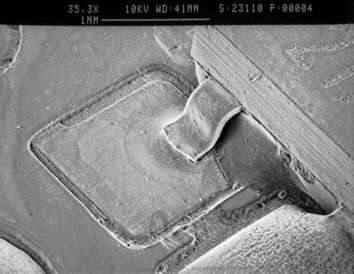
SEM
Insufficient solder at SOT-223
Description:
Insufficient solder at the (wide) front lead. The reflow process could not produce an acceptable solder fillet at the heel of the lead.
Causes/Remedy:
- Reflow soldering: too few / poor solder paste applied
- poor wetting at the lead
- unsuitable process temperature
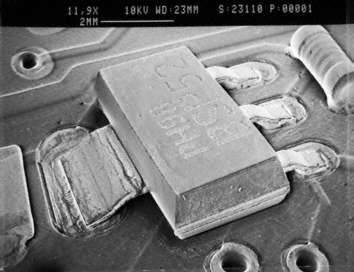
SEM
Description:
Magnification of the previous example. The poor solder fillet at the heel is clearly visible.
Causes/Remedy:
- poor/insufficient solder paste applied
- wetting problems at the lead
- unsuitable process temperature
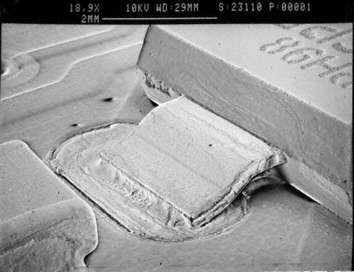
SEM
Description:
The leads on the other side also reveal problems with the solder fillet. Here the solder joints are acceptable though.(IEC 61191-2)
Causes/Remedy:
- poor/insufficient solder paste applied
- wetting problems at the lead
- unsuitable process temperature
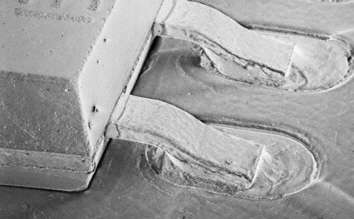
SEM
Insufficient solder, general
Description:
Insufficient solder at a HMT solder joint. The solder applied is - with reference to 61191-3 - smaller than 75% of the wettable area. Therefore the solder joint has to be reworked.
Causes/Remedy:
- poor flux / flux application
- poor process parameter (soldering angle, temperature)
- bad wettability of board/pads
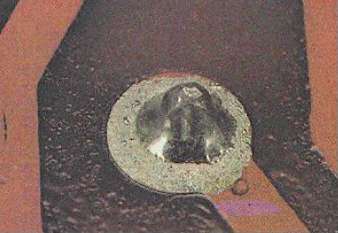
visual, optical inspection - general view
Our analytics team can help you find the cause.
go to failure analysis at TechnoLab