The original structure of the solder paste is still visible. Particular risk: Electrical tests normally deliver the result PASS.
Not completely molten solder paste at CMC
Description:
Defect very distinct: The solder joint on the left is not completeley molten in comparison with the one on the right. It can also be clearly seen rhat the surface tension of the solder in molten condition affects the component (component at an angle). Rework necessary.
Causes/Remedy:
- poor soldering profile (reflow)
- shadow effect during IR-reflow
- partial heat gaps due to faulty layout (design)
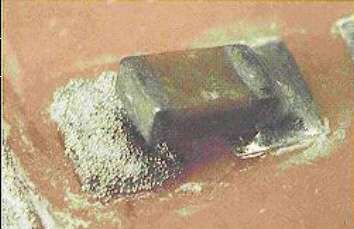
visual, optical inspection - general view
Not completely molten solder paste at SO
Description:
Solder paste not completely molten at a SO component. The area near the edges (in front) still shows the ball-like structure of the solder paste. Rework necessary (re-heating).
Causes/Remedy:
- poor soldering profile (reflow)
- shadow effect during IR-reflow
- partial heat gaps due to faulty layout (design)
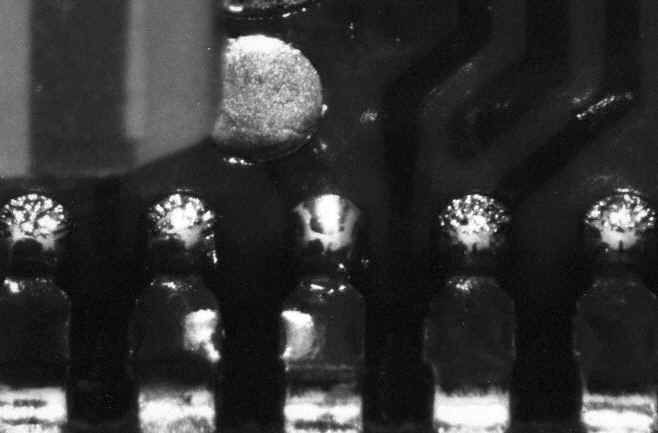
visual, optical inspection - general view
Solder paste not completely molten at SOT23
Description:
Solder paste not completely molten at a SOT23. Again the solder paste structure is still distinct.
Causes/Remedy:
- poor soldering profile (reflow)
- shadow effect during IR-reflow
- partial heat gaps due to faulty layout(design)
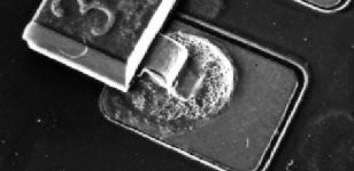
SEM
Description:
General view of the above example. The solder joint at the through-hole has completely molten.The defect indicates a poor heat distribution for parts of the assembly (layout fault)
Causes/Remedy:
- poor soldering profile (reflow)
- shadow effect during IR-reflow
- partial heat gaps due to faulty layout (design)
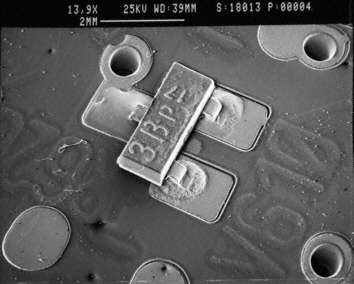
SEM
Our analytics team can help you find the cause.
go to failure analysis at TechnoLab